DIY Amplifier, Vacuum Tube Category
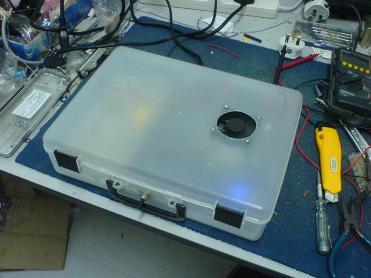
READ THIS FIRST!
Don’t just jump straight into DIY amplifier yet! Before we get started, we need to make sure we adhere to the DIY amplifier processes in order to avoid complications in the later stage. Spending more time now will reward us and prevent us from failure! Take this from a guy who had walked the rushed path before and regretted it till today.
Let’s do it right the first time! Here are the major steps:
- Wants & needs analysis
- Research & design amplifier
- Expandability and design for test
- Planning & sourcing for components
- Build and finishing
- Testing & tuning for good sound
- Installation and setting up in your system
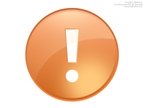
Wants & needs analysis
What are your wants and needs in DIY tube amplifier? “Wants & needs” dictate what you’d like to build, in terms of internal (sonic) and external (outlook) characteristics. It also depends on your listening taste, environment, partnering equipment, setup biasing, and etc. Different tubes, circuits, components, output power, tuning and etc will affect the sound and look. Therefore, one needs to know all these before they go further into the DIY process.
There are slight differences between wants & needs. Want is what you desire, what you intended to have. Need is what you and your system requires. For example, if you like very brightly lit vacuum tube amplifiers – you can choose tubes with tungsten filaments. It has no relationship at all to what you need. Need is something like the output power required to drive your speakers sufficiently to fill your listening with sound or music. Need is something like the number of sources you have, therefore commanding the equivalent number of inputs to your amplifier.
Let’s move on. In this phase, you will get to know and define the following:
- Output power requirement:
- Size of the listening room – bigger -> higher power
- Speaker sensitivity – higher -> lower power
- Listening volume / behavior – louder -> higher power
- Type of music – more dynamic -> higher power
- Note 1: For vacuum tube amplifier, general rule is, the lower the power, the simpler the design, the smaller the size, the shorter the signal path, the lesser the coloration, the better it sounds.
- Note 2: The first Watt is the best Watt for usual vacuum tube amplifier.
- Distortion / noise / hum tolerance
- Different designs / circuits have different distortion behavior, noise level and hum level on an tube amplifier. How you layout will also affect these parameters and change the amplifier sound.
- Note 1: Single ended amplifiers usually have higher even harmonics and lower odd harmonics – that, to some, equals warmer, sweeter and mellower sound. Higher odd harmonics means more hifi-ish, steely or hard sounding.
- Note 2: AC heating sounds the best but for some tubes, especially for those with direct heated filament tubes, sometimes DC heating is necessary to reduce hum / noise level to a tolerable level.
- Functionality/ usage model
- How do you intend to use your DIY amplifier? Long hours? Enclosed space? Long cabling? Public Addressing? Bedroom use? Background music? Ventilation scheme? Long life? Durability? Serviceability?
- Pre / power / integrated / buffer – these need no introductions, right? Sometimes integrated are preferred for the cost and conveniences – single chassis takes up less space and cost for components and interconnects prices.
- Functions – What other audio functions are needed apart from amplification? Tone controls, equalizer, active crossover, bypass, loudness, integrated DAC, phono amplifier, speaker protection, short circuit protection, remote control, bi-amping, wireless transmission, and etc?
- Environment – Does it need to be reliable and durable? Is the ambient temperature high or low? Will it be subjected to moist, vibration and movements? This will determine the electrical and thermal design of the amplifier to fulfill the normalized working hours and temperature of the system. Temperature and heat buildup are always something that needs to be considered and calculated in a design.
- Note: These will affect how the amplifier is designed to match the usage model and functionality.
- Sonic characteristics / tastes
- Topology – single ended, push-pull, interstaged, class (A, A2, A/B, D), 2-3-4 staged, solid state rectifiers, tube rectifiers, constant current sources, and etc – different type of topologies have their own kind of sound.
- Character – warm, powerful, hifi, fast, mellow, dynamic, and etc. All these characteristics are tunable, by the design, implementation, component usage, cabling, and etc.
- Component selection is a big topic by itself. When you’re experienced enough, you will know that different types of components have different character. Use the ones that suit your taste!
Choose your own poison!
- Cost / budget
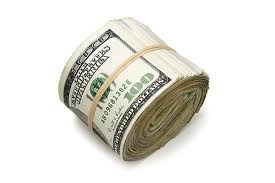
- $$$ - the amount of $$$ allocated will determine what type of design you can have, and whether can you go for audiophile or non-audiophile components, of course, with a premium.
- Remember this: garbage in, garbage out! Please do not expect stellar performance if you skimp on the quality. If budget is limited, focus on those parts that bring the most return, highest ROI. For a tube amplifier, it could be the vacuum tubes, output transformer, PSU, capacitor, and such.
- One can think about using exotic materials and components too and make your tube amplifier unique, only one of the kinds in this world! Life is just too short to be plain and boring!
- Size & weight – Simpler design, lighter weight, smaller size vice versa. Different design, different component requirement, different weight, different size and different price!
- Visual – higher cost, better looks! One can even choose to have cat’s eye tubes and vacuum tubes with tungsten filament to look better – for example the 10, 801, and 801A vacuum tubes.
- Connections
- Types of I/O: speaker terminal types, input/output jacks, balanced, unbalanced, USB input, SPDIF input, pre-out, bi-wire, stereo jack, headphone jack, phono input, iPod docking port and etc, audiophile / non-audiophile versions.
- Front/back panel: decide what needs to be in front and what needs to be at the back panels. This will impact how you layout your amplifier blocks in the chassis.
- Partnering equipment
- Speaker impedance – 4 Ohm, 8 Ohm, 16 Ohm, impedance characteristics (dips, rises, even). For vacuum tube amplifiers, high impedance with lesser dips speakers is highly recommended.
- Damping factor requirement – This has impact on how good the amplifier can control the speakers. It doesn’t mean that the higher the figure, the better it is. Different speakers require different numbers.
- Input level & type (input sensitivity) – higher input level requires lesser overall gain at the amplifier side. Know your partnering equipment and you will save a lot of energy in the amplifier design.
- Safety is number one!
- This is the MOST important factor you need to think about! If you are unsure of what you’re doing, do not do it! Tube amplifier contains high LETHAL voltages!
- Safety can be on yourself, your family, your pets, your environment, your setup, and your wallet!
- If you’ve young family members or pets around the house, then you’ve to design your system to be accident proof.
- If you’re inexperience in dealing with electricity, then, hire an experience and qualified electrician to help you. Or, do not do it at all. Life is more important than hobby itself.
- Any voltages can be lethal! Choose the voltages you’re comfortable on working with. I myself would avoid anything that has too high voltage. Anything below 600Vdc is still OK with me. This could be different with each individual.
- What I mentioned above is neither comprehensive nor complete. So, take precaution and be extra careful when you are working with electricity.
DIY tube amplifier is starting to get complicated, isn’t it? Feel lost? Don’t understand all? Don’t be afraid. If you do not know what you want, just go look and listen around to see what you like, determine your tube amplifier requirements, or just for the fun of DIY, “Just do it”!
After you’re clear on what you needed and wanted on your analysis above, the real fun begins! It always takes me the longest time to research and design my own amplifier. There are just soooooo many designs out there and soooo many things to consider.
R&D here could be applied here to the chassis design, amplifier design, layout design, system design, thermal design, and etc. Think about it makes me feel high! I’m a natural born R&D engineer! The fun part about this is, instead of being limited to what other people designed, you can decide on your own! No one knows yourself better!
Finalizing one to build is really a big joy, or headache! :P Take your time here. You will be handsomely rewarded if you put enough care and effort in this, and the planning phase.
Expandability and design for test
Whenever you build your amplifier or system, always think about these 2 words – expandability & DFT (Design For Test).
Leave some room for expansion. One will never know what might arise in the future, or even during the construction process! Something might go wrong and demand for space for further / future upgrades, tweaks, or even correction!
On the other hand, always layout and make your amplifier as testable as it can be. After you finished building your amplifier, what comes next is the testing phase. Even after the system is in service, one might need to service or tune it if some components break down, or the tubes go weak. Or even when someone helps you to troubleshoot your amplifier.
All these require thoughts and planning prior to the construction.
Planning & sourcing for components
This could be the fun part for some, and pain in the *** for some. LOL. I, for one, love sourcing for parts, minus the act of taking out my credit card or hard earned cash to pay for them. LOL.
Sourcing is just like cooking! Think of what to cook, and go get all the ingredients. The fresher and better the ingredients, the better your dish would be. Once the design is finalized, you can start listing out all the required parts in a spreadsheet and categorize them:
- Hardware
- Electrical & electronics
Hardware could be chassis, screws & nuts, spanner, screwdrivers, saw, hole punch, drill & bits, and etc.
Electrical & electronics could be wires, capacitors, resistors, inductors, fuses, I/C, tubes (yes!), multimeters, LCR meter, oscilloscopes, spectrum analyzer, distortion analyzer, and etc.
All these can be obtained at your local stores, our bought online. There are mainly 2 types of stores, audiophile and non-audiophile versions. Non-audiophile versions could just be like Maplin, Mouser Electronics, Radioshack, RSWWW, Farnell, and those general hardware, electrical & electronics stores. Audiophile ones are those that cater for mostly audio related components, and usually they carry a premium due the better sound quality and marketing strategy of the shops.
I use a mixture of audiophile and non-audiophile components. Audiophile components do bring better sound quality no doubt! I use generic components for those less critical (to sound reproduction) areas and splash on those important sections like the coupling capacitors, output transformers, vacuum tubes and such.
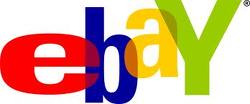
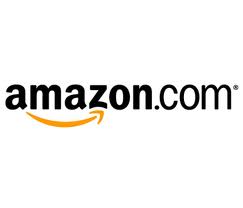
Even eBay and Amazon are good sources for components!
Build and finishing
How do you want your DIY project to look? Like a “DIY project” or professionally finished? We’re quite lucky nowadays as there are lots of shops now selling finished or semi-finished amplifier chassis. The materials range from aluminum, mild steel, to stainless steel. My personal favorite are aluminum as they’re easier to work with but pain in the *** to finish.
Finishing options are plenty as well, like paint, plating, brushed, powder coated and such. Different finishing has their pros and cons. Recently I like buying semi-finished (brushed aluminum) chassis for my projects. They’re less hassle to work with.
One can even hire or commission someone to build the tube amplifier chassis for you. I do use this option some of the time since I’ve several friends who are in this line. They can use CNC machine to build me nice metal and wood based chassis with a charge.
If you want your DIY tube amplifier finishing to look nice, make sure you plan your hardware work properly. Defects on the surfaces will ruin the finishing and give you more hard work if you want to make it look nice later. So, use care and do not remove the protective covers (some do come with it) until you’re happy and finalized your project.
Testing & tuning tube amplifier for good sound
Have you used, or even heard of multimeters, oscilloscope, spectrum analyzer, frequency generator / synthesizer, distortion analyzer, and such? Don’t worry! We shall give you a briefing on them too in this website. For now, just remember that they will be your best friends in the DIY amplifier world.
The MOST basic equipment one should own is the multimeter. You can live without the others but this is a MUST. It will be used to check the inductance, capacitance, resistance, open / short, frequency, voltage (AC & DC) and etc of your DIY amplifier.
When a project is completed, we shall use the multimeter to check the DIY amplifier to make sure everything is built according to the design. After we powered-up the project, we shall use the multimeter to check for correct voltages and biasing of the amplifier.
How do we tune the tube amplifier sound? This is a very difficult question! This can be done through many, many ways! It is impossible to cover it all in just the briefing / introduction section. We shall share with you on the tuning as we post more DIY projects or DIY amplifier projects in this website.
These are just a few ways on how we tune the sound and is not comprehensive:
- Circuit biasing
- Circuit design
- Vacuum tube
- Components usage
- Chassis and hardware
- Placing and routing
- Electrical isolation & filters
- Mechanical isolation
Installation and setting up in your system
Congratulations! You’ve come to the stage of installing and setting up your tube amplifier in your system. You’ve come a long way and I’ve gotta give you a pat on your back, and tell you “Good job mate!”. Nothing beats listening to your own hand crafted project for the 1st time. I’m sure it would be a great looking and sounding project too if you put enough effort into making it.
All right! This sums up what we’ve to say on DIY amplifier. We shall cover more on those topics in the later phase. This is just the introduction!
Since I’ve just finished DIY tube amplifier: 5687 IT coupled 6B4G integrated amplifier to power the Zu Soul Superfly (101dB/w/m) , I will use that as the reference or example to illustrate the whole process.
Return from DIY Amplifier to DIY Tube Amplifier